From labels on products to logistics labels for shipping, stickers are indispensable in many business processes. Imagine: the label is stuck and the roll is empty. Where do you leave the sticker sheet? In the residual waste? Or are there more sustainable options?
In this blog series, our Zero Waste Officer Milan takes on the challenge of office waste to discover innovative solutions for each waste stream. In this blog, he focuses specifically on the waste stream released from sticker sheets. Are you reading along?
The challenge of the material
Sticker sheets consist of two parts: the sticker and the sticker sheet itself, also called the backing or liner. Both parts are made of different materials and require different approaches when it comes to processing and recycling. Milan takes a closer look at both parts.
The sticker and sticker sheet
Stickers are often made from a combination of paper and a thin layer of plastic, usually polyethylene (PE) or polypropylene (PP). This plastic layer is applied to make the sticker stick better, and to make it resistant to moisture, dirt and abrasion.
Besides the sticker itself, a sticker sheet, or backing, always remains after use. This backing is the sheet to which the stickers are attached until they are used. The backing is usually made of silicone-containing paper or plastic. The silicone layer allows the stickers to easily detach from the sheet, which is important for the functionality of the product.
However, this combination of paper and plastic throws a spanner in the works of recycling. A plant that specializes in paper cannot properly process the plastic layer, while plastics plants again have trouble with the paper fibers. This means that stickers, after use, are not suitable to be recycled into a new sticker or sticker sheet.
As a result, many Dutch stickers end up in incinerators after use, where they contribute to harmful emissions. Abroad, stickers can also end up in landfills. There they break down very slowly into small pieces that end up in the environment.
The size of the waste stream
Although specific figures are hard to come by, it is estimated that millions of tons of sticker sheets end up in the waste stream worldwide each year. Especially in industries where large quantities of products are packaged and shipped, such as logistics, retail and manufacturing, the use of sticker sheets is high. In these industries, it is standard to use stickers to label boxes, pallets and individual products. Each of these stickers leaves a backing, and all those backings add up to a significant waste stream. In most cases, they are considered regular industrial waste and end up in the black bin, residual waste.
Alternatives to with sticker sheet material
Our Zero Waste Officer investigated more environmentally friendly alternatives to traditional sticker sheets and shares a number of promising options, some of which are already being tested in practice. Are you reading along?
Compostable Stickers
Some companies are experimenting with fully compostable stickers made from materials such as cellulose, a natural component of plants. These stickers can break down completely in industrial composting environments, so they have no long-term impact on the environment.
Sticker sheets made from bioplastics, such as PLA (Polyactide)
Bioplastics, such as PLA (polylactide), can be used as an alternative to traditional polyethylene (PE) or polypropylene (PP). However, PLA (Polyactide) is degradable only in an industrial plant, and then also under very strict conditions. Thus, it is not the case, that you can throw a PLA (Polyactide ) sticker sheet into the environment, and thus does not guarantee that it will be properly recycled.
Sticker sheets made of paper
People are also experimenting with all-paper sticker sheets. These are made from recycled paper, but again contain a coating. Although paper is easier to recycle, this coating hinders recyclability.
In addition, paper is more susceptible to tearing and abrasion. Thus, with paper, the user will need to put on a new sticker sooner. Furthermore, these stickers are less resistant to heat, cold and moisture. In that respect, too, paper sticker sheets are much less durable. This can be a problem when the stickers are exposed to outdoor conditions, such as shipping labels or product labels. It is also not desirable in medical environments.
Reusable labels
Reusable labels can also be considered for certain applications. These are stickers that can be used multiple times as they can be easily removed and reapplied without loss of adhesive strength. While not suitable for every industry, they can provide a solution to reduce waste for internal logistics applications, for example.
Downcycling of sticker sheets
In addition to alternatives to the material of sticker sheets, there is another option looking at recycling options. This involves converting sticker sheets into hygiene paper, such as tissues or toilet paper. This process is also known as downcycling because the recycled material results in a lower quality product than the original product. Despite the silicone coating, companies such as WEPA can separate the paper portion from the non-paper portions.
Although downcycling is a step in the right direction to reduce waste, it is not the preferred sustainable solution. This is because with each recycling process, the material degrades in quality, meaning it eventually becomes unusable for further processing. The result: it still becomes waste. Therefore, circular recycling is preferred, where materials retain their original properties and can be reused over and over again, providing a more sustainable solution in the long run.
Zero Waste solutions
Our Zero Waste Officer had his eye on two notable, more sustainable innovations. He is happy to tell you more about linerless stickers. He also explains direct printing.
- Linerless stickers are an innovative solution that omits the traditional backing (liner) of stickers, resulting in less waste and lower costs. These labels are becoming increasingly popular because of their sustainability and efficiency benefits, especially in industries such as retail, logistics, and food packaging.
- Direct printing means that the information is printed not on a label, but directly on the box. There are handy devices on the market for this purpose. This reduces the waste of labels by large increments, as well as the time an order picker spends on the sticker sheet.
The benefits
We list the main advantages of these solutions:
- Waste reduction: Since there is no more sticker sheet, the amount of waste is significantly reduced. Linerless stickers can generate up to 50% less waste compared to traditional stickers; direct printing even up to 100%. So, apart from the ink you need for direct printing, this method is Zero Waste, if you use it smartly.
- Cost savings: the above solutions use less or even no material. This not only reduces waste, but also saves costs in terms of material consumption, transportation, and storage.
- Efficiency: both direct printing and linerless stickers can save time. With linerless stickers, more stickers fit on a roll. This reduces the need for businesses to replace rolls, which increases productivity. This makes them especially useful in busy environments such as warehouses and distribution centers.
- Versatility: Linerless stickers are increasingly used in the food industry, retail and logistics. In supermarkets, they are often used for labeling products such as meat and vegetables, with the labels automatically adjusting to the product information. Direct printing is also increasingly used in e-commerce and logistics, where large volumes of packages are processed daily. Both technologies play an important role in sectors where speed and flexibility are important.
The disadvantages
Aside from all the advantages, these solutions are not suitable for every industry. Milan lists:
- Linerless labels designed for short-life applications, such as shipping labels, receipts, or price labels. For labels that need to stick in challenging environments, such as outdoors or when exposed to moisture and heat, traditional labels may be more durable and reliable. In addition, Linerless labels can sometimes suffer from adhesive problems. Because they have no backing, they can stick together more quickly during printing or storage. This sometimes complicates processing and can lead to inefficiencies, such as mislabeling.
- While direct printing offers many advantages, it is not always the best option when information on the label must be changed frequently, such as the order number or delivery address. Because it prints directly on the package, it is difficult to make changes without restarting the entire process. This makes direct printing less suitable for applications where flexibility in data is necessary.
Idea or solution? We'd love to hear it
Returning to the question of whether sticker sheets unnecessarily end up in residual waste, we can confirm that this is not the case. The stickers often contain a combination of paper and plastic, and the backing usually contains paper or plastic with silicone. Therefore, they should almost always be disposed of with the residual waste. This is the most common method of disposal for materials that are not suitable for regular recycling streams.
Fortunately, innovative developments and alternatives are on the rise to improve product recycling.
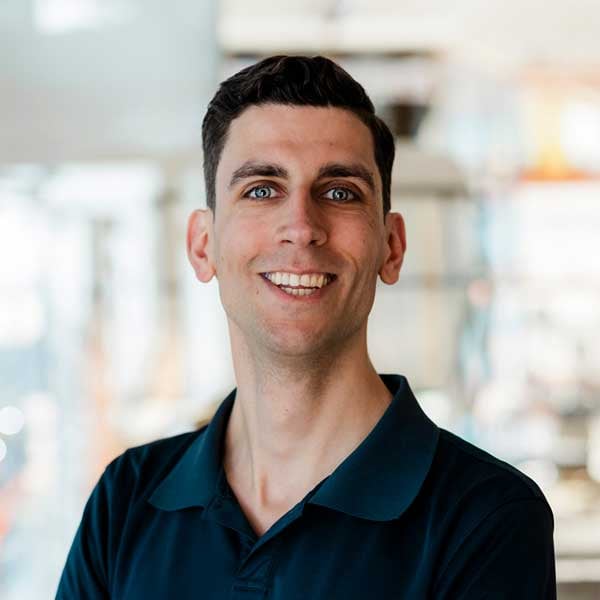
Vraag het onze Zero Waste Officer
Twijfelt u of bepaalde items binnen uw kantoor onnodig in het restafval belanden? Milan helpt u graag verder. Stuur uw vraag naar marketing@milgro.nl en wie weet gaat hij op zoek naar innovatieve oplossingen.
Op de hoogte blijven
Op de hoogte blijven van alle nieuwe ontwikkelingen? Volg ons op LinkedIn en Instagram of abonneer u op de nieuwsbrief. Bent u nieuwsgierig naar wat Milgro voor uw bedrijfsvoering en afvalproces kan betekenen? Neem dan contact op.